发动机的重量在乘用车整车中占12%左右。发动机的轻量化,可以提高汽车动力性、节省材料、降低成本,并涉及整车的质量分布。发动机的轻量化必须保证在以工作可靠性和整车安全性为前提下,通过材料、工艺、结构的优化设计达到轻量化目标。
一、发动机轻量化途径
发动机轻量化技术途径是通过结构优化和使用轻质材料。
(1)通过拓扑优化分析相关零件结构并进行尺寸优化和形状优化,降低零件重量并同时降低零件成本。
(2)通过不同零件功能组合,进行零件模块化设计,减少零件数量,提高模块通用性。
(3)采用先进的轻量化材料技术、加工设备及成型工艺技术实现汽车发动机产品零件的轻量化。
(4)在具体实施的过程中应采取概念设计先行,材料与工艺相辅相成的技术路线。
二、结构优化
目前在发动机设计研发行业里,发动机集成化、轻量化是设计的主流方向,同时,发动机零部件的结构创新和优化对装备和工艺也提出了新的要求。下面列举几个结构创新的例子。
1.气缸盖集成排气歧管
近年来,无论是大众第三代EA888,还是现代的Kappa,又或是通用的Ecotec,在这些发动机上都不太容易找到排气歧管。难道这些发动机都不需要排气歧管吗?其实这些发动机并没有将排气歧管抛弃,而是巧妙地将排气歧管集合在了发动机缸盖里,这样从外部看起来发动机仿佛就没有了排气歧管(图1红色部分)。
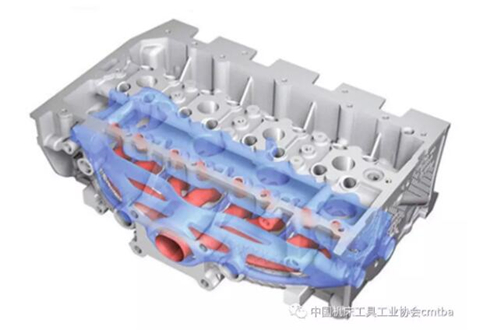
图一
由于这项技术将排气歧管集成于气缸盖内,排气歧管内的热废气能够更好地与缸盖水套进行热交换,这样同是采用发动机冷却水来冷却,相当于冷却系统多了一个热源,能够更快地实现暖机,减少冷启动造成内部构件的摩擦,使发动机更快地进入高效工作状态,从而达到降低排放,节省油耗的目的。
由于内置式气缸盖排气歧管也起到了简化发动机零部件的作用,从而能让发动机减少3-5kg的重量,同时减少的重量位于发动机顶部,所以这对于整车的重心降低是有所裨益的。
日产汽车公司的VR30DDTT发动机机型的气缸盖将排气歧管与原气缸盖集成为一体(见图2)。由此,能在气缸盖的排气出口处布置涡轮增压器,使得催化器可布置在气缸盖附近。其结果表明,该举措能大幅提升起动后催化器入口的排气温度,使催化剂活性时间减少50%左右。另一方面,在排气温度较高的条件下,利用气缸盖内的散热能有效降低排气温度。
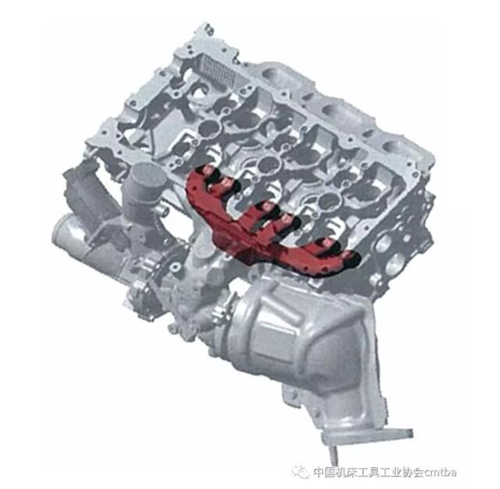
图2
2.瘦身连杆
EA888发动机连杆的结构优化也十分明显,在确保工件强度和刚性的前提下, 其杆部至围绕大头孔部分都进行了瘦身。若取杆部中截面观察, 呈清晰的“工”字形。小大头孔部的上、下端面,在极大多数情况下都为一组平行面, 经结构优化后的这部分形状变成了锲形。其他还有若干处也体现了去重、优化,如连杆小大头孔凸缘部分的削薄处理以及取消孔内的铜套(见图3)等。
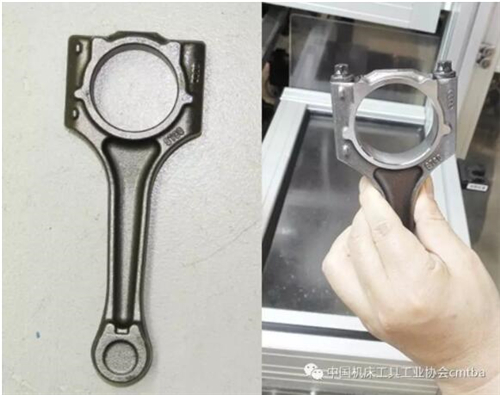
图3
3.空心凸轮轴
传统的一体式凸轮轴采用单一的材料,通过铸造或锻造制坯后经多工序切削加工而成。而在凸轮轴轻量化工作中,主要是将其空心化。空心凸轮轴有三种方式:加工式空心凸轮轴、铸造空心凸轮轴、组装式空心凸轮轴。
上汽大众EA888采用组合式空心凸轮轴。这种凸轮轴是由铁基粉末冶金材料制成凸轮,然后用烧结或机械的办法将凸轮固定在空心钢管上。与铸铁件相比,中空装配式凸轮轴减轻质量25-30%,在降低生产成本、提高整机性能等方面具有传统凸轮轴无法比拟的优势,越来越受到广泛关注和重视,并成为凸轮轴制造技术的发展方向。
4.缸体铸造油道
传统缸体回油道是通过机械加工方式从缸体顶部打通到曲轴箱内部,对加工刀具的要求较高。同时缸顶较窄油孔直接对着曲轴,溜回的润滑油直接到高速运转的曲轴上,增加了曲轴的阻力。另外,回油道铸造缸体对增加缸体的整体强度,增加缸体的抗变形能力起到很好作用,缸体就可以做得更紧凑。
发动机缸体铸造成型油道是新型发动机的发展趋势,这种缸体采用常规水平浇注很困难,目前采用组芯、立浇工艺较多。立浇工艺有两种:一种是纯组芯工艺,直接浇注,这种方法现场环境难以保证;第二种是组芯与造型线结合生产工艺,即建立壳芯生产线。
5.利用3D打印技术优化结构
雷诺卡车公司新设计了一款4缸5L发动机,由于一些零部件采用3D打印技术,其质量减少了120kg,并且相关零部件的耐久性已经得到测试验证。截至目前,雷诺卡车公司的工程师已虚拟设计了完整的发动机,其摇臂和凸轮轴轴承盖采用金属3D打印制造,并在台架上顺利地对这款欧Ⅵ发动机进行了600h的测试。
3D打印制造技术给内燃机提供了全新的发展前景,使得制造商可以利用分层材料制造零部件,并减轻装配操作强度和优化发动机部件数量。这种技术最大的好处是便于整合和优化零部件。雷诺卡车公司新开发的发动机,零部件数量减少200个,相当于减少了25%。工程师集成了80个缸体零件和45个缸盖零件。与此同时,他们还优化了交流发电机和发动机线束的支架。
6.曲轴的轻量化
上汽大众发动机曲轴的结构优化,已在技术允许的情况下把工件的减重、轻量化做到了极致。所采取的主要措施有:减少扇板数量,从传统的8片减少到4片;减小扇板的宽度,并进行形状优化;缩小主轴颈的尺寸,平均缩小10%,如对两款系列产品中的一同类型发动机(1.6L MPI),EA111机型的主轴颈外径为50mm,EA211则减为40mm;在每个连杆轴颈上加钻了去重孔。其他细节上的结构优化还有很多。如此,两者在自重上相比,新一代EA211发动机的曲轴重量较之EA111平均要减轻15-20%。
另据报道,天津一汽夏利内燃机制造分公司经过技术创新,在国内首先开发出主轴颈、拐颈为空的中空曲轴,使得曲轴重量降低15%。
7.活塞的轻量化Borgo Nova公司为BMW轿车2.0L 6缸发动机开发了一种轻型X形活塞,在裙部、销孔座及相应膨胀部位呈明显的X形状,如图4所示。左侧表示轻型X形活塞,右侧为传统收缩窗式活塞。X形活塞重量减轻100g,而其压缩高度、连杆长度不变,同时活塞摩擦面积减小,从而降低了机械摩损和单位燃油消耗。整体组装后,X形活塞比传统收缩窗式活塞减重96g,即17.0%。
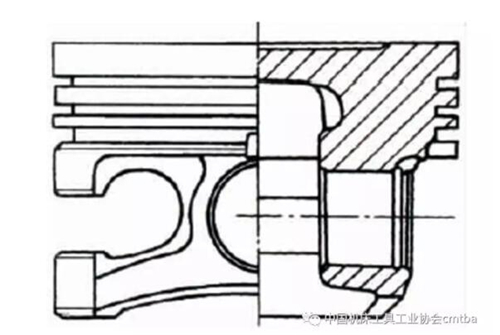
另外,一些发动机附件在轻量化方面也有文章可做,如博格华纳量产的新型轻量化静音链系统,在链条、张紧器、SIFF(Slide In Flat Face)中分别作了材料、设计及工艺的优化,帮助整个新型链系统减轻重量。其采用8mm/6.35mm链板材料的齿形链,在保持其强度、耐磨性及NVH特性不变甚至提高的情况下,减轻重量提高传动效率。就链条本身而言,减轻25-30%的重量。链系统中的张紧器采用了优化设计方案,减轻10-20%重量。SIFF也减轻结构设计,并对工艺做了从注塑成形到挤压成形的优化,其重量减轻30-40%。
三、材料创新
发动机轻量化在材料方面首先是考虑用铝合金材料、镁合金材料替代密度大的铸铁材料,在优化改进结构的基础上实现结构更强,质量更轻。高强度结构钢使零件设计得更紧凑和小型化,有助于汽车的轻量化,主要应用于气门弹簧、齿轮、涨断连杆等。铝合金主要应用于气缸体、缸盖、活塞、进气管、水泵壳、起动机壳体、摇臂、发动机支架、滤清器底座、齿轮室罩盖、飞轮壳、油底壳等发动机零部件。镁合金主要应用于链条室、气门等。
根据美国铝学会的报告,汽车上每使用0.45kg铝就可减轻车重1kg,理论上铝制汽车可以比钢制汽车减重40%。
1.铝合金加工中的工艺创新——缸孔喷涂技术
随着汽车朝轻量化方向发展,铝合金发动机在汽车行业的应用比例越来越高。由于铝合金的耐磨性和力学性能不如铸铁,因此传统的铝合金发动机必须镶嵌铸铁缸套,以提高性能。但是铸铁缸套的缺点在于缸套和缸体之间的封装,由于两种材料热容性特征不同,会影响铝质发动机缸体的耐用性。对此,国外已研发出一种新的工艺技术——缸孔喷涂技术,也可称为无缸套技术。
缸孔喷涂技术是采用热喷涂技术(电弧喷涂或等离子喷涂)对经过粗化处理的铝发动机缸孔内壁喷涂一层合金涂层或者其他复合材料,取代传统的铸铁缸套(见图5)。喷涂了涂层后的铝合金缸体依旧是一体式缸体,涂层的厚度仅有0.3mm,具有降低发动机重量、降低缸孔与活塞的摩擦和磨损、提高热传导、降低油耗和二氧化碳排放等优点。
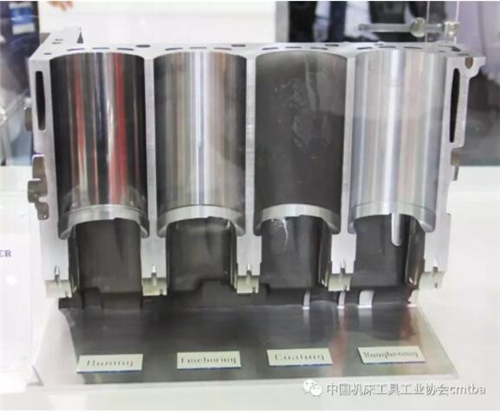
热喷涂视频
2014年,日产在1.6L 4缸MR16DDT发动机上采用了电弧喷涂的气缸孔镜面涂覆技术(MBC),MBC技术使用电弧喷射工艺替代等离子喷涂工艺。电弧喷射工艺可在气缸工作表面上形成许多小的气孔,即使没有进行珩磨网纹槽加工,这些气孔也会储有润滑油。其结果表明,采用表面粗糙度为Ra0.05µm级的镜面精加工,除了能提高抗爆燃性能之外,对于降低气缸孔与活塞间的摩擦也有良好效果。
2.蠕墨铸铁缸体缸盖
蠕墨铸铁是一种高强度材料,它的力学性能和铸造工艺性能介于灰口铸铁和球墨铸铁之间,很适合制造强度要求较高、且要求承受热循环负荷的零件,如气缸体、气缸盖。蠕墨铸铁的高强度,说明汽缸可以在压力更高的环境下工作,更容易实现尾气排放的要求;其次,发动机更能满足轻量化的需求,更具紧凑性,从而更符合重型柴油机缸体材料的发展趋势。一台装配好的蠕墨铸铁发动机的重量一般要比灰铸铁发动机轻9%左右。
国6阶段的技术升级重点表现在热效率、爆压,喷射压力的提升,后处理技术多样化,动力多元化发展等领域。进一步提升发动机热效率,是未来5-10年国内外发动机技术持续改进的重要方向之一。国6阶段中国柴油机行业热效率为46-48%,国6后将提升为50-55%。蠕墨铸铁的大量应用将助推国6阶段的技术升级。现在,国内几个大型柴油机企业开始批量应用蠕墨铸铁缸体缸盖。
但蠕墨铸铁加工比较困难,对刀具的要求较高。造成蠕墨铸铁难以加工的原因主要有以下几个方面:
(1)蠕墨铸铁热传导率较低,加工时产生的切削热积聚在工件中,加剧刀具磨损。
(2)蠕墨铸铁零件的铸造硬皮具有铁素体结构,容易与刀具切削刃发生粘结作用。
(3)与灰铸铁不同,蠕墨铸铁中不含硫化物,无法像灰铸铁中的硫化物一样,可以沉积到刀具切削刃上对刀具起到润滑作用。
(4)在蠕墨铸铁的铸造工艺中,加入了钛作为合金元素,会产生了强度较高的铸造外皮,同时在整个铸件中形成了具有磨蚀性的游离碳化物,也对其可加工性以及刀具寿命产生不利影响。
(5)蠕墨铸铁强度较高,一般要比灰铁加工高30%左右的切削功率。
由于上述原因,用于切削蠕墨铸铁的刀具寿命通常只有切削灰铸铁刀具寿命的一半,甚至更低。
3.非金属材料的应用
发动机材料大部分为优质铸铁、结构钢或铝合金,但随着材料技术的发展,一些复合材料也开始在发动机上应用。
发动机油底壳作为储油槽的外壳,用于收集和储存润滑油并保证散热。目前,绝大多数的汽车油底壳主要为冲压成型的钢制油底壳或压铸成型的铝合金油底壳,但也有部分企业开始应用玻纤复合材料。
玻纤增强复合材料的密度比钢材和铝合金的密度都要小,所以能够有效降低零部件的质量,而且通过注塑成型可以实现收集器、机油滤清器及机油挡板等的集成,进一步减少空间占用、生产制造费用和装配费用。从汽车轻量化的角度出发,与铸铝油底壳相比,结构优化后的玻纤增强复合材料注塑成型油底壳的质量降低了37.16%,实现了轻量化设计。
另外,气歧管塑料化也是汽车轻量化的要求。塑料进气歧管不仅质轻,而且由于内壁光滑,可改进气体流动性,提高气体流量,进气效率高,隔热效果好,因而能提高发动机性能和燃料利用率。由于焊接技术的提高,可制作从简单到复杂的塑料进气歧管,把复杂的进气歧管分片注塑成型,利用振动摩擦焊接组焊成型。分片注塑结构工艺优化,可降低模具成本,避免注塑制品缺陷,提高制品性能。
四、结语
发动机轻量化是一个复杂的系统工程,它涉及到从设计到材料,再到工艺等多个方面。相对整车轻量化来讲,发动机轻量化要求更高,实施起来更加困难。不仅如此,发动机零件众多,特别是排放升级,发动机增加了一些必要的外附件,每增加一个部件都会增加发动机的自重。因此,发动机轻量化会面临更多的挑战。